这些年来,随着物联网、大数据、工业互联网、数字仿真技术、虚拟现实技术、GIS/BIM技术的持续发展,数字化工厂孪生的建设已经从概念阶段逐步得到落地。各制造行业的标杆企业,为了全面提升企业竞争力,着力通过对真实工业生产的全流程进行虚拟规划、仿真优化,进而实现对工厂产品研发、制造生产和服务的全面优化和提升,将现代工业化与信息化有机融合,向智能制造迈出重要一步。从广义来说,“数字化工厂孪生”不但涵盖了从产品设计、工艺规划、生产制造到售后服务保障的产品全生命周期的整个价值链的创造过程,还包含了在全周期中的企业管理过程。这整个过程中企业信息化和工业化的相互融合,真实世界和虚拟世界的不断迭代、相互促进,使企业制造的智能化得到不断提升,实现整个价值链的增值。数字化工厂的架构如下图所示:
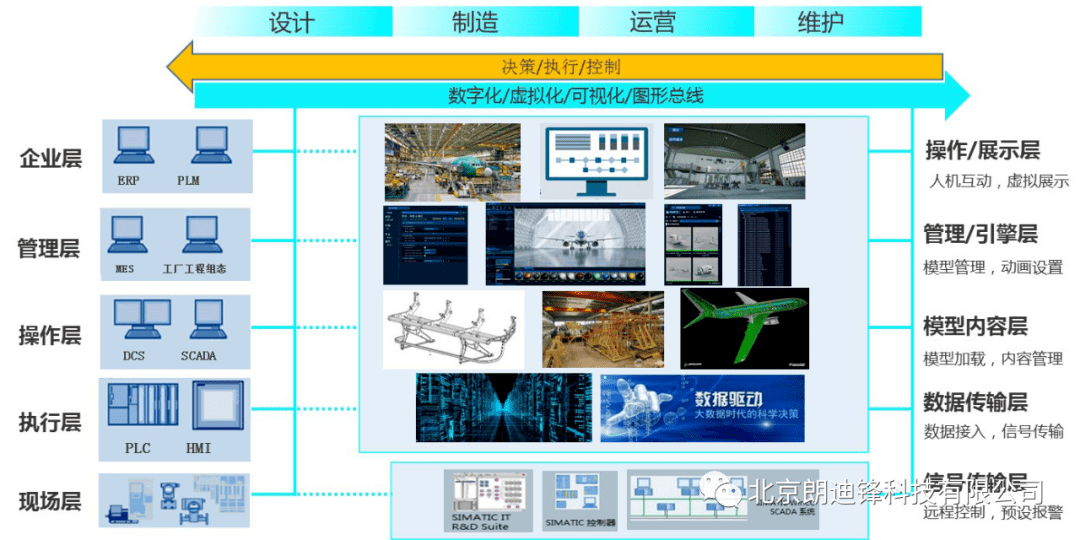
如上图所示,数字化工厂有五层架构:(1)现场层:包括传感器、仪器仪表、条码、射频识别、机器设备装置,以及电力、燃气能源设施等硬件;(2)执行层:与硬件设备紧密相关的可编程逻辑控制器(PLC)、人机交互(HMI)等等;(3)操作层:数据采集与监视控制系统(SCADA)、分布式控制系统(DCS)和现场总线控制系统(FCS)等控制系统,是制造企业进行生产的技术基础;(4)管理层:包括面向设计部门的产品数据管理(PDM)、面向工艺部门的工艺工装管理、面向生产部门的制造执行系统(MES)、面向后勤保障部门的能源管理系统等等;(5)企业层:包含了产品生命周期管理(PLM)、企业资源计划系统(ERP)、供应链管理系统(SCM)和客户关系管理系统(CRM)等等,实现企业价值链的管理。此外,随着5G和云技术的发展,企业通过互联网共享信息实现企业各部门间的协同,甚至产业链上下游的协同,也使数字化工厂孪生的应用上升到新的层面。
数字化工厂孪生的建设不但需要实现生产设备之间的互联互通,还有设备和产品的互联。由设备组成生产线,生产线连接组成数字化车间,数字化车间互联成数字化工厂孪生,而不同地域的数字化工厂孪生组成企业级数字化制造系统,未来不同企业的数字化工厂孪生还可以组成产业链级的数字化制造联盟。最终,通过虚拟世界和现实世界的互联,将虚实世界中的设备、生产线、工厂、供应商、产品、客户紧密地连接在一起。
数字化工厂孪生的落地,本质上是实现数据信息的融合,通过云计算、大数据、虚拟现实等新一代信息技术,在保障数据安全的前提下,实现产线调试、动态工厂模拟优化、工厂展示、培训演练、实时监控、数据信息共享以供决策等功能。
2图2 运用虚拟产线进行监控
数字化工厂孪生的建设需要四大核心技术:建模与压缩技术,仿真技术,数据集成技术,GIS、BIM、大数据、云等多种技术的融合应用。1、建模与压缩技术:
数字化工厂孪生最大的特点就是产品设计和生产均可在数字化空间中虚拟进行,这样不仅可以对产品设计可行性进行仿真验证,还可以对新产品进行可制造性和制造成本提前预估分析。要实现上述功能首先要建立从厂区、厂房、车间、产线到设备等等实物的虚拟模型。虽然当前三维建模技术已经相对成熟,但是一个企业从厂区到设备级的模型往往来自不同建模软件,且模型大小各不相同,如果没有专业的集成工具,如何将其在虚拟场景中集中呈现都成为一道难题,更别说使其如真实场景中一般运行。
为此,北京朗迪锋科技有限公司开发了专门的虚拟产线可视化工具——MakeReal3D PlantiViz,该工具运用独特的模型轻量化算法(见图3),能将不同来源的三维模型大幅度轻量化,不但实现了将三维模型快速导入,还将模型在平台中统一格式,以便于三维数据的管理:
图3 MakeReal3D PlantiViz对常用三维原生模型大幅轻量化并实现快速导
仿真优化是数字化工厂孪生的价值核心,根据虚拟模型和仿真系统呈现出的运行状态及各种管理数据,判断、分析真实工厂中可能出现的各种问题和潜在的优化方案,进而优化产品设计和生产过程,因此呈现出的状态和数据越逼真,越能够有效支持决策和优化。
MakeReal3D PlantiViz以世界领先的的虚拟现实引擎为基础,并内置了面向工业制造业的高精度物理引擎,因此无论对于静态还是动态的产品、加工过程、产线/车间/工厂规划过程、制造管理过程等等,都能完美呈现和仿真。
图4 MakeReal3D PlantiViz真实呈现设备结构和特性和精确的设备运动仿真
图5 实时呈现真实产线加工过程
3、数据集成技术
在产品的全生命周期中,存在着不同部门和用途的各种数据,如设计、工艺、制造、采购、销售、服务等各个环节的数据,来自于前述架构中从现场层到企业层五个层次的系统。为了支持决策和优化,将这些数据实时呈现于虚拟工厂中,是数字化工厂孪生落地必须要面临的挑战。而朗迪锋公司的MakeReal3D PlantiViz产品,以其良好的开放性和兼容性,正成为虚拟工厂建设者们进行多系统数据集成的有力工具。
图6 MakeReal3D PlantiViz通过OPC数据通讯协议集成多系统现场数据,并实现虚实产线之间的交互
4、GIS、BIM、大数据、云等多种技术的融合应用近年来,随着5G通信和云计算技术的落地,以及三维实景技术的迅猛发展,使大型集团企业级甚至供应链级的数字孪生成为可能。在数字安全管理的前提下,上述各产线、车间、工厂,甚至企业的孪生场景和地理位置均可真实呈现,并实现其间的互联互通和交互,实现企业内管理数字化的提升,亦可实现企业间相关业务、流程与共享资源的数字化,从而使企业具备参与供应链数字化管理和敏捷制造的能力。
由于大型集团企业的分支机构以及供应链上下游的地理位置都分布广泛,工业、企业园区的厂区、仓储、车间等相关制造设施和供应链设备的时间和空间分布,需要从宏观层面上解决空间化、数字化、孪生化,而三维实景地理空间信息无疑对企业和供应链的宏观运转产生重要影响,是企业宏观决策的重要考虑因素之一。所以从集团企业级和供应链级的孪生建设来看,需要将分布在不同区域的、多角度的地理空间信息进行集成。为此,北京朗迪锋科技有限公司与埃洛克航空科技(北京)有限公司建立了战略合作伙伴关系,将大型集团内部以及供应链上下游的三维实景空间地理数据,与工厂、厂房、产线、设备等中、微观数据和各管理系统数据进行集成,形成基于数字化工厂孪生的PAAS平台解决方案。这种解决方案的实现,无疑将为客户提供更加完善、战略性的决策依据,从而为企业创造更大社会价值和经济价值。 某大型汽车集团为了提高汽车制造体系竞争力,在企业内部建立数字化制造实验室,储备了先进的数字化虚拟制造技术,为企业降本增效、提高核心竞争力提供有力的保障。该企业在建立数字化制造实验室之前,从企业层面看,从产品设计到生产制造的各个阶段,涉及到很多不同格式的数字化资源信息。如何系统高效地管理这些信息,使其在企业价值链前端(产品设计)及后端(生产制造)发挥最大作用,保证产品可制造、易制造、工艺精益,是数字化虚拟制造技术面临的巨大挑战。该车企通过对虚拟现实技术攻关,首先在MakeReal3D平台上实现多个数据来源——产品结构设计CAD数据、仿真CAE等数据的集成可视化,以加速产品设计的决策流程,避免了多系统切换的问题。通过虚拟的可拆卸、可装配、可维修性实验、人机工效仿真替代物理实验,加速了产品研发过程,同时减少物理样机的制造周期和成本。而后通过对数字化制造技术的研究,利用MakeReal3D PlantiViz工具在真实工厂调试之前,率先在软件环境中实现工艺、机器人、控制程序的集成调试,实现虚拟世界到真实世界的无缝转化,减少现场调试时间,提高项目实施质量。通过车间现场的实时数据和工艺规划设计过程中使用的3D模型互通,达到车间设备再利用,产品质量在线监控,设备能耗在线监控。进而在生产过程中,降低操作工的劳动强度,提高生产效率;优化生产线操作工数量;减少非增值时间,优化增值时间,以最终实现智能制造,精益生产和提高质量。
图7 在MakeReal3D PlantiViz中运用虚拟产线进行调试
该企业通过数字化工厂孪生项目的实施,实现了如下效果:1、生产线设计阶段,在虚拟的环境中,可以通过模拟信号的输入、停顿,来测定信号在传输过程中所需要的真实时间,保证模拟生产与实际生产节拍的一致性。2、生产线设计阶段,对将要安装调试的生产线进行虚拟调试,降低在线调试风险。在优化工艺的同时,提高产品试生产通过率,降低问题整改费用、缩短产品试生产时间(约50%)、降低调试能耗。3、产能提升或多车型共线柔性化生产时,通过在数字工厂环境中模拟仿真,更加准确的验证和分析方案可行性、线体融合度、新品通过率等,实现改进方案的准确制定和优化。4、当现场出现质量问题时,可以通过虚拟环境中的资源、数据对现场的问题进行仿真验证,寻找真因,减少过程中的资金投入,缩短现场解决问题的时间。